Blog
The new OHS policy rewards people who are merited in occupational health and safety matters
25.06.2024
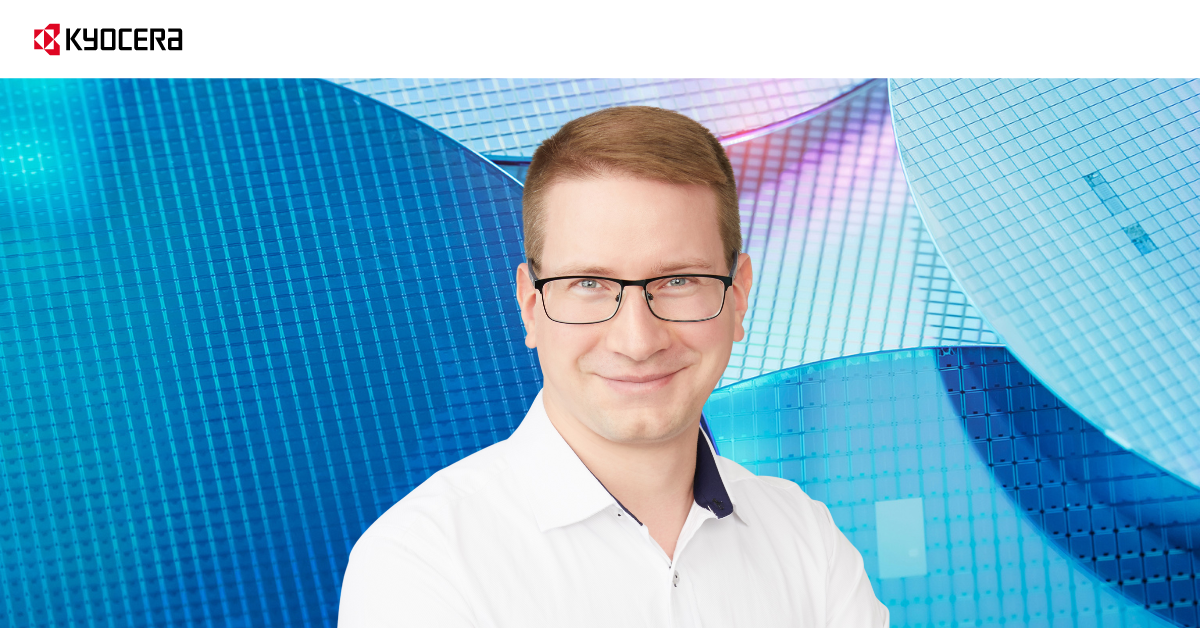
Did you know that 18% of accidents happen at workplaces? The number is not very high, but usually most of the accidents could be avoided with constructive dialogue between employer and employees. By investing in the training and skills of employees, and by using suitable protective equipment, even dangerous methods can be applied safely. That’s why we have decided to start giving rewards to people who are merited in occupational health and safety matters. Our OHS Manager Hannu Heikkinen tells more about our new OHS policy.
Occupational safety is a continuous process
I started writing a new occupational health and safety policy for Kyocera Technologies from a clean slate. I reflected on my own experiences with occupational safety and health, as well as on issues that arose during the training of the occupational safety and health manager. Finally, I also considered the requirements of legislation.
The key thing in occupational safety is that improving occupational safety is a continuous process. On the other hand, the situation in general is not particularly bad in Finland at the moment, because only 18% of accidents happen at workplaces (Uhritutkimus 2017, THL). The aim, of course, is to ensure that no accidents occur at workplaces at all.
Occupational health and safety are always the art of compromise. How to invest in occupational health and safety so that the work of an individual employee does not become difficult or unpleasant? For example, if the use of protective equipment is very unpleasant, there is a significant risk that it will not be used, or at least its use will be avoided. Therefore, it is always advisable to discuss the use of protective equipment and related practices with the employees and develop occupational safety continuously.
Investing in the OHS pays off
Kyocera works with semiconductors, and the methods required in research activities can be very dangerous if misused or in the event of an accident. This sets the bar high when discussing Kyocera’s occupational safety.
Working closely with other organizations also brings its own perspective. We cooperate strongly with the Finnish state-owned research institution VTT, because some of our work is done in facilities managed by VTT. The advantage of this is that VTT’s strong expertise in occupational health and safety matters is at our disposal. At the same time, it places a strong demand on communication: since there are several different companies in the same space, it is important that everyone operates by the same rules.
On the other hand, history has shown that by investing in the training and skills of employees together with suitable protective equipment, even dangerous methods can be used safely.
People have a tendency to behave in a certain way if there are suitable incentives to do so. At the suggestion of our Managing Director, I added to our OHS policy a mention that a person who has merited in occupational health and safety matters can be rewarded – also financially. At the same time, it emphasizes how important occupational health and safety issues are for us and that we are ready to invest in them.
Who is Hannu Heikkinen?
Hannu works as an Equipment Engineer and OHS Manager at Kyocera Technologies.
His most important job as Equipment Engineer is to take care of and maintain our different tools containing complex technology. In other words he is responsible for everything working as it should. At the same time, he plays an important role in acquiring new tools. Hannu has a degree in chemical engineering and he says his academic background suits well for the second role as OHS Manager.
“We are dealing with various chemicals every day so it’s important to know what you are dealing with,” he says. “As OHS Manager I also take care of our protective equipment and arrange training sessions related to occupational safety. I also wrote our Occupational Health and Safety Policy document.”
Hannu has been a part of our team for over a year. He says there has been a lot to learn, particularly at the beginning, but his previous experience has been very helpful in taking on the new role.
According to Hannu, the semiconductor industry is a very interesting field. The most rewarding moments are when you get to solve a problem with the team:
“If, for example, one tool is broken it’s the best feeling when you figure out what the problem is and how to fix it,” Hannu says. “This company is very compact so the decision-making process is very efficient. On the other hand we don’t have many experts in the same team so everyone has more responsibility.”
When he is not at work, you might see Hannu driving a taxi or at the meetings of Espoo City’s Technical Services Committee.